|
|
|
|
|
|
|
|
|
|
|
|
|
|
|
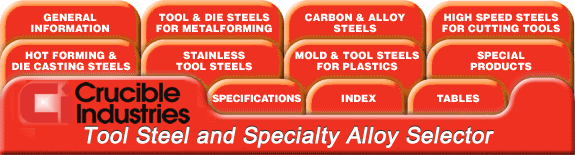 |
|
|
REX M2®S (1.0C)
(AISI M2)
|
|
|
 |
|
|
REX M2S (1.0C) is a sulfur-bearing high carbon version of the regular CRUCIBLE REX M2 high speed steel. The sulfur addition provides good grindability and an improvement in machinability of 25 to 35 percent over a comparable nonsulfurized grade. The increase in carbon content produces higher attainable hardness, increased wear resistance and red hardness which contribute to significant gains in cutting tool performance. The higher carbon offers improved hardenability in larger tool sections.
|
|
|
|
|
|
Typical Chemistry |
Carbon |
1.00% |
Manganese |
0.30% |
Silicon |
0.30% |
Chromium |
4.15% |
Vanadium |
1.95% |
Tungsten |
6.40% |
Molybdenum |
5.00% |
Sulfur |
0.10%
|
|
Typical Applications |
|
Broaches |
Reamers |
|
Form Tools |
Shaving Cutters |
|
Gear Hobs |
Spade Drills |
|
Milling Cutters |
Tool Bits |
|
|
|
|
|
|
|
|
|
|
|
|
- Annealed Hardness: BHN 229/255.
Machinability in the annealed condition is approximately 45% of W1 Tool Steel (1%C).
Thermal Treatments
Critical Temperature: 1525F(830C).
Forging: 2075F(1135C) Do not forge below 1700F(925C). Slow cool after forging.
Annealing: 1600F(870C), hold 2 hours, slow cool 25F(15C)/ hr max. to 1000F(535C), then air or furnace cool. Hardness BHN 229/255 Stress Relieving: 1100-1300F(595-740C), hold 2 hrs. and air or furnace cool.
Straightening: Best done warm 400-800F(205-425C)
Hardening: (Salt Baths or Vacuum Furnace preferred)
Preheat: 1500-1550F(815-845C), equalize
High Heat: 2100-2200F(1150-1205C), soak 2 to 5 minutes. For vacuum hardening, use the high side of the high heat range and soak times.
Quench: Salt or oil to 1000-1100F(540-595C), equalize, then air cool to hand warm, 150F(65C). Temper immediately. The vacuum quench rate to below 1000F(540C) is critical to achieve comparable results.
Temper: Tempering at 1000F(540C) or higher times for at least 2 hours at temperature is recommended. Air cool to room temperature between tempers.
|
|
|
|
|
|
|
Hardening Data
Oil quenched. |
|
Tempering
|
Hardness HRC
|
Temperature
|
2175F
(1190C)
|
2200F
(1205C)
|
°F
|
°C
|
|
1000
|
540
|
66
|
66
|
OPTIMUM FOR MAXIMUM TOUGHNESS AND EFFECTIVE STRESS-RELIEVING.
|
1025
|
550
|
65.8
|
66
|
1050
|
565
|
65.2
|
65.5
|
1075
|
580
|
63.8
|
64.3
|
1100
|
595
|
62
|
63
|
1125
|
605
|
|
61
|
|
|
|
|
|
|
|
|
|
|
|
|
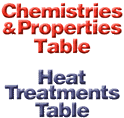 |
|
|
|
|
|
|
Size Change During Hardening |
|
- Hardening
- Temp.
|
- Tempering
- Temp.
|
HRC
|
- Longitudinal
- Size Change
%
|
°F
|
°C
|
°F
|
°C
|
|
2200
|
1204
|
1025
|
552
|
65
|
+.23
|
|
|
|
|
|
|
|
|
|
|
Surface Treatments
REX M2S (1.0C) can be nitrided, steam tempered, or titanium-nitride coated if desired. If the CVD TiN treatment is used, care is required in vacuum hardening.
Physical Properties
Modulus of Elasticity ...................................................................30 psi x 106 (207 GPa)
Specific gravity ............................................................................................................8.15
Density .......................................................................................0.294 lb/in3 (8150 kg/m3)
Coefficient of Thermal Expansion
- Temperature
- Range
|
- Coefficient of Thermal
- Expansion
|
°F
|
°C
|
in/in/°Fx10-6
|
mm/mm/°Cx10-6
|
70-500
|
21-260
|
6.40
|
11.5
|
70-800
|
21-425
|
6.58
|
11.8
|
70-1000
|
21-540
|
6.72
|
12.1
|
|
|
|
|
|
|
|
|
|
Return to top of page
|
|
|
|
|
|