|
|
|
|
|
|
|
|
|
|
|
|
|
|
|
|
|
|
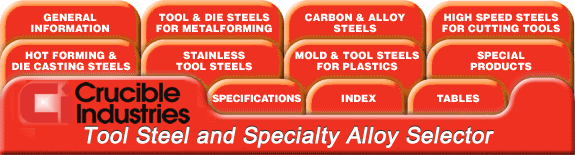 |
|
|
|
|
KAPSTAR® |
|
|
|
 |
|
|
|
|
|
Kapstar is a high hard, precipitation hardening mold steel suitable for production of machined or EDMd plastic mold, rubber mold, and zinc die casting die components. Kapstar is supplied at about 40 HRC and further heat treating is generally not required. It is a through-hardened steel that exhibits uniform hardness through thick and thin sections. It is easily machined, polished, textured, and welded.
|
|
|
|
|
|
Typical Chemistry |
Carbon |
0.12% |
Nickel |
4.00% |
Manganese |
1.50% |
Vanadium |
0.10% |
Sulfur |
0.10% |
Silicon |
0.40% |
Chromium |
0.50% |
Copper |
0.20% |
Molybdenum |
0.25% |
Aluminum |
1.00% |
|
|
Typical Applications |
|
Plastic Injection Molds |
Tool Holders |
|
Blow Molds |
Rubber Molds |
|
Zinc Diecasting Dies |
Composite Molds |
|
Pressure Plates |
Stripper Plates |
|
|
|
|
|
|
|
KAPSTAR® is a registered trademark of Nippon Koshuha Steel Co., Ltd. |
|
|
|
|
|
|
|
|
|
- Hardening
Kapstar is supplied prehardened at 37-42 HRC. Further heat treating is normally not required.
Surface Treatments
Kapstar is highly suitable for nitriding. Nitriding should be done at 1000-1040F (540-560C) and furnace time should not exceed 72 hours, or softening will occur. Nitriding will result in surface hardness of 60 HRC and higher. If tools have thin or sharp sections, avoid long furnace soaks and use a quick 6-12 hour cycle instead. This will produce a hard, wear-resistant surface approximately .001"-.002" (.025-.050mm) deep and will prevent brittle areas from forming.
Stress Relieving
Kapstar is a stress free steel; stress relieving is neither needed nor recommended.
Welding
The use of Kapstar weld wire is recommended for the best results; in an emergency AWS E 9018 3L can be used.
Pre-heat to 570-750F (300-400C) in a furnace; if not using a furnace, pre-heat slowly. Maintain above 570F (300C) during welding.
Post-heat immediately at 1000F (540C) for five hours to re-age the heat affected zone to 40 HRC. No quenching or tempering is necessary.
If you have a large weld, to reduce distortion, the mold must be solution treated at 1510-1550F (820-845C) for three hours, air cooled, and then re-aged at 1000-1040F (540-560C) for five hours immediately after welding.
|
|
|
|
|
|
|
|
Physical Properties
Modulus of Elasticity ...................................29.9 psi x 106 (206 x 103Mpa)
Density ..................................................................0.282 lb./in3 (7806 Kg/m3)
Thermal Conductivity
RT .............................................. 15.2 BTU/hr/ft/F (22.2 Kcal/mhrC)
212F(100C)...............................16.2 BTU/hr/ft/F (24.1 Kcal/mhrC)
392F(200C)...............................16.9 BTU/hr/ft/F (25.3 Kcal/mhrC)
572F(300C)...............................18.1 BTU/hr/ft/F (26.9 Kcal/mhrC)
Thermal Expansion
|
|
|
|
|
|
|
|
|
|
|
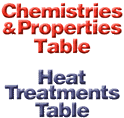 |
|
|
|
|
|
|
|
|
- Temperature
- Range
|
- Coefficient of Thermal
- Expansion
|
°F
|
°C
|
in/in/°Fx10-6
|
mm/mm/°Cx10-6
|
RT-212
|
100
|
5.1
|
9.1
|
RT-392
|
200
|
6.2
|
11.1
|
RT-572
|
300
|
7.0
|
12.5
|
RT-752
|
400
|
7.5
|
13.6
|
|
|
|
|
|
|
|
|
|
|
Return to top of page
|
|
|
|
|
|