|
|
|
|
|
|
|
|
|
|
|
|
|
|
|
|
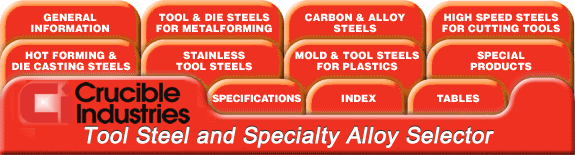 |
|
|
CPM® 15V
|
|
|
 |
|
|
|
CPM 15V is Crucibles highest vanadium, abrasion resistant CPM tool steel. It contains 50% more hard vanadium carbides in its microstructure than CPM 10V, to provide even higher wear resistance.
CPM 15V is intended for applications requiring exceptional wear resistance. Applications where CPM 10V is successful, but even longer tool life is desired, or applications where sintered carbide tooling is prone to fracture or difficult to fabricate, are likely to be well-served by CPM 15V.
|
|
|
|
|
|
Typical Chemistry |
Carbon |
3.40% |
Manganese |
0.50% |
Silicon |
0.90% |
Chromium |
5.25% |
Vanadium |
14.50% |
Molybdenum |
1.30% |
Sulfur |
0.07% |
|
Typical Applications |
|
Powder Compaction Tooling: |
|
Punches, Dies, Core Rods |
|
Plastic Processing Equipment: |
|
Barrel Liners, Screw Tips, Wear Inserts |
|
Dies and Punches for: |
|
Forming, Cold Extrusion, Drawing, Piercing |
|
Industrial Knives |
Granulator Blades |
|
Slitter Knives |
Woodworking Tools |
|
Ceramic Dies |
Wear Parts |
|
|
|
|
|
|
|
|
|
|
|
- Annealed Hardness: BHN 255/277.
Machinability in the annealed condition is slightly more difficult than 10V. SG type alumina wheels or CBN wheels are recommended for the best grinding performance with the CPM steels.
Thermal Treatments
Critical Temperature: 1540F(838C).
Forging: 2000-2100F(1095-1150C) Do not forge below 1700F(930C). Slow cool.
Annealing: 1600F(870C), hold 2 hours, slow cool 30F(15C)/hr max. to 1000F(540C), then air or furnace cool. Hardness BHN 255/277.
Stress Relieving (After machining): 1100-1300F (595-740C), hold 2 hrs. and air or furnace cool.
Hardening: (Salt, vacuum or atmosphere)
Preheat: 1500-1550F(820-845C), equalize. Second preheat stage at 1850-1900F(1010-1040C) suggested for vacuum or atmosphere hardening.
High Heat: 1950-2150F(1065-1175C). Standard recommendation to achieve 60-62 HRC after tempering for a good combination of wear and toughness is to use 2050F(1120C).
Quench: Salt, oil or atmosphere quench to 1000-1100F(540-595C), equalize, then air cool to below 125F(50C) or hand warm. Vacuum or atmosphere quench rate through 1850-1300F(1010-705C) range is critical to achieve optimum heat treat results.
Straightening: Best done warm 600-1000F(315-540C).
Temper: 1000F(540C) minimum recommended. Double tempering is required.
Stress Relieving (Hardened Parts): Temper 30F(15C) below original tempering temperature.
|
|
|
|
|
|
Hardening Data
|
|
Tempering
|
HEAT TREAT RESPONSE
|
Temperature
|
2050F
|
2100F
|
2150F
|
°F
|
°C
|
(1120)C
|
(1150)C
|
(1175)C
|
|
As Quenced
|
65
|
64.5
|
63
|
1000
|
540
|
62
|
63
|
64
|
OPTIMUM FOR MAXIMUM TOUGHNESS AND EFFECTIVE STRESS-RELIEVING.
|
1025
|
550
|
60
|
62
|
63
|
1050
|
565
|
58
|
60
|
61
|
1100
|
595
|
54
|
55
|
56
|
1150
|
620
|
48
|
50
|
51
|
1200
|
650
|
46
|
47
|
48
|
|
|
|
|
|
|
|
|
|
|
|
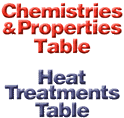 |
|
|
|
|
|
Size Change During Hardening |
|
- Hardening
- Temp.
|
- Tempering
- Temp.
|
HRC
|
- Longitudinal
- Size Change
%
|
°F
|
°C
|
°F
|
°C
|
|
1950
|
1065
|
1000
|
540
|
60
|
+.04
|
2150
|
1175
|
1000
|
540
|
64
|
+.05
|
|
|
|
|
|
|
|
|
|
|
Surface Treatments
CPM 15V can be nitrided or titanium-nitride coated if desired. If the CVD TiN treatment is used, care is required in vacuum hardening.
Physical Properties
Modulus of Elasticity ...................................................................32 psi x 106 (221 GPa)
Specific gravity ............................................................................................................7.41
Density .......................................................................................0.268 lb/in3 (7418 kg/m3)
Coefficient of Thermal Expansion
|
|
|
|
|
|
|
|
|
- Temperature
- Range
|
- Coefficient of Thermal
- Expansion
|
°F
|
°C
|
in/in/°Fx10-6
|
mm/mm/°Cx10-6
|
70- 200
|
21-93
|
5.96
|
10.7
|
70-500
|
21-260
|
6.18
|
11.1
|
70- 800
|
21-427
|
6.54
|
11.8
|
70-1100
|
21-593
|
6.82
|
12.3
|
|
|
|
|
|
|
|
|
|
|
|
Return to top of page
|
|
|
|
|
|